Welcome to Paul Plucinsky’s group website! We are a research group studying the mechanics of materials and structures — with an overarching theme of examining the interplay between material and structure. Particularly, we aim to understand and predict the interesting mechanics and functionality that emerges when complex materials — such as active and architectured materials — are incorporated into thin or slender structures. This poses several challenges: State-of-the-art materials science research is producing novel materials with active and architectured features at many length scales, rendering engineering scale prediction of their often highly non-linear behavior difficult at a purely computational or experimental level. The challenges are then compounded when these materials are incorporated into inherently non-linear thin and slender structures. To address these challenges, we work at the intersection of engineering mechanics, materials science and applied mathematics with the goals of:
Examples of our research are highlighted below. For more detailed descriptions, feel free to view the Research page.
Research Vignettes
-
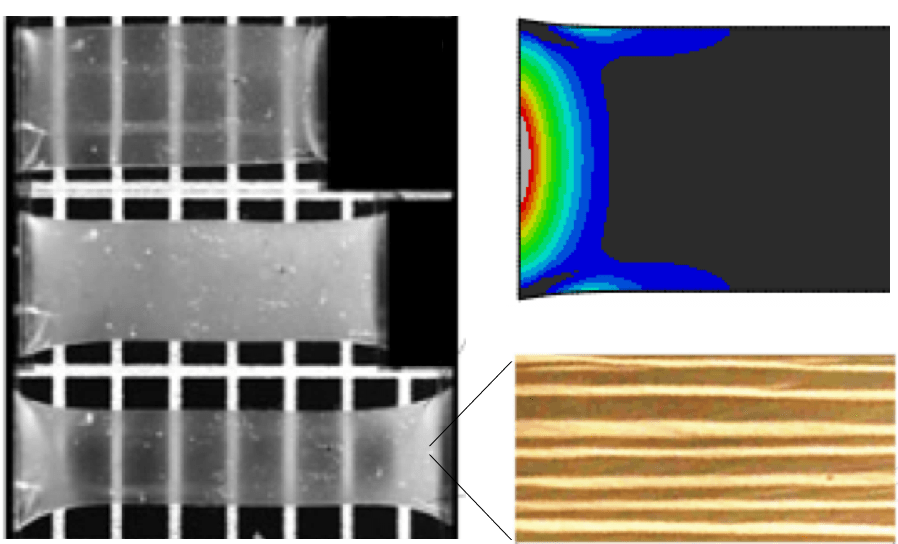
The clamped-stretch experiment of Kundler and Finkelmann (1995) on nematic elastomers sheets (left). While sheets of conventional materials typically wrinkling under this loading, the nematic elastomer sheet here forms strip-domain microstructure on a very fine scale (the cloudy regions) and does not wrinkle. Our modeling and simulation efforts helped to explain this phenomenon.
-
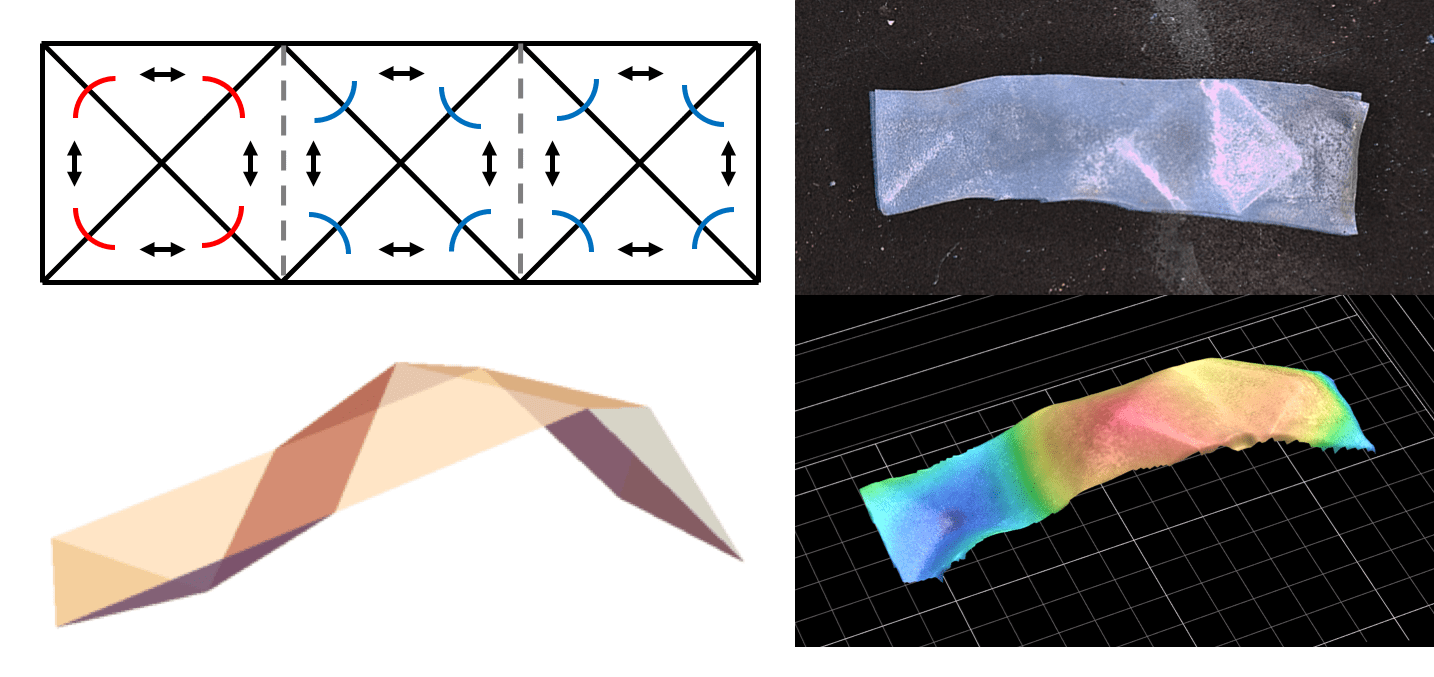
Nematic elastomers can be programed to deform anisotropically under stimuli. By carefully designing this anisotropy into thin sheets, one can actuate complex shape from simple building blocks. We developed a theory for doing this via nonisometric origami. The left figure is an example of a design in this framework and its predicted actuation. The right is an experimental realization of this actuation strategy (courtesy of our experimental collaborators Ben Kowalski and Timothy J. White).
-
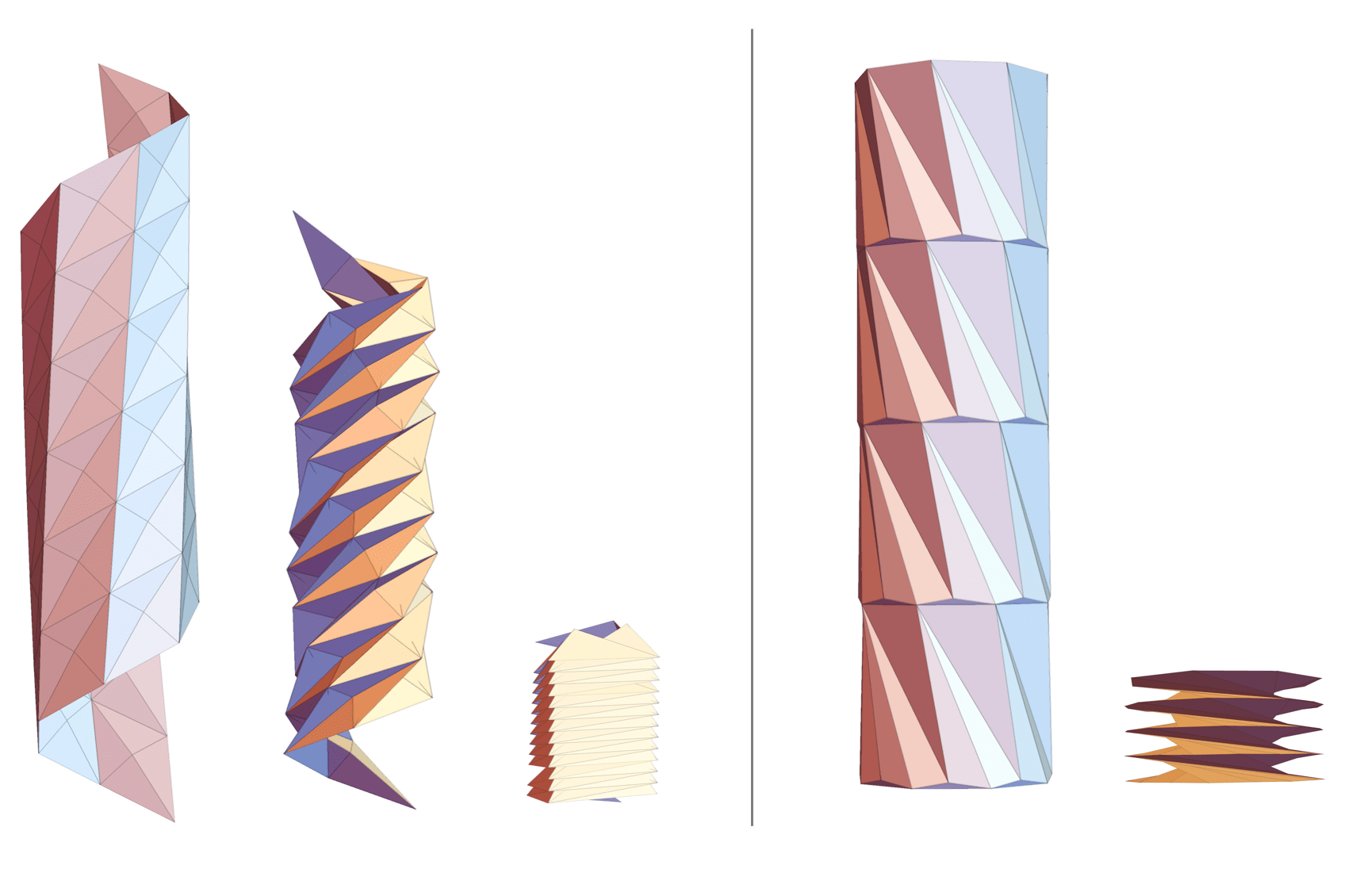
Examples of multi-stable cylindrical origami. Through suitable mechanical loading, each structure displayed can transform from one of its stable states to another. This results in dramatic twist and contraction (or extension) of the overall structure.
-
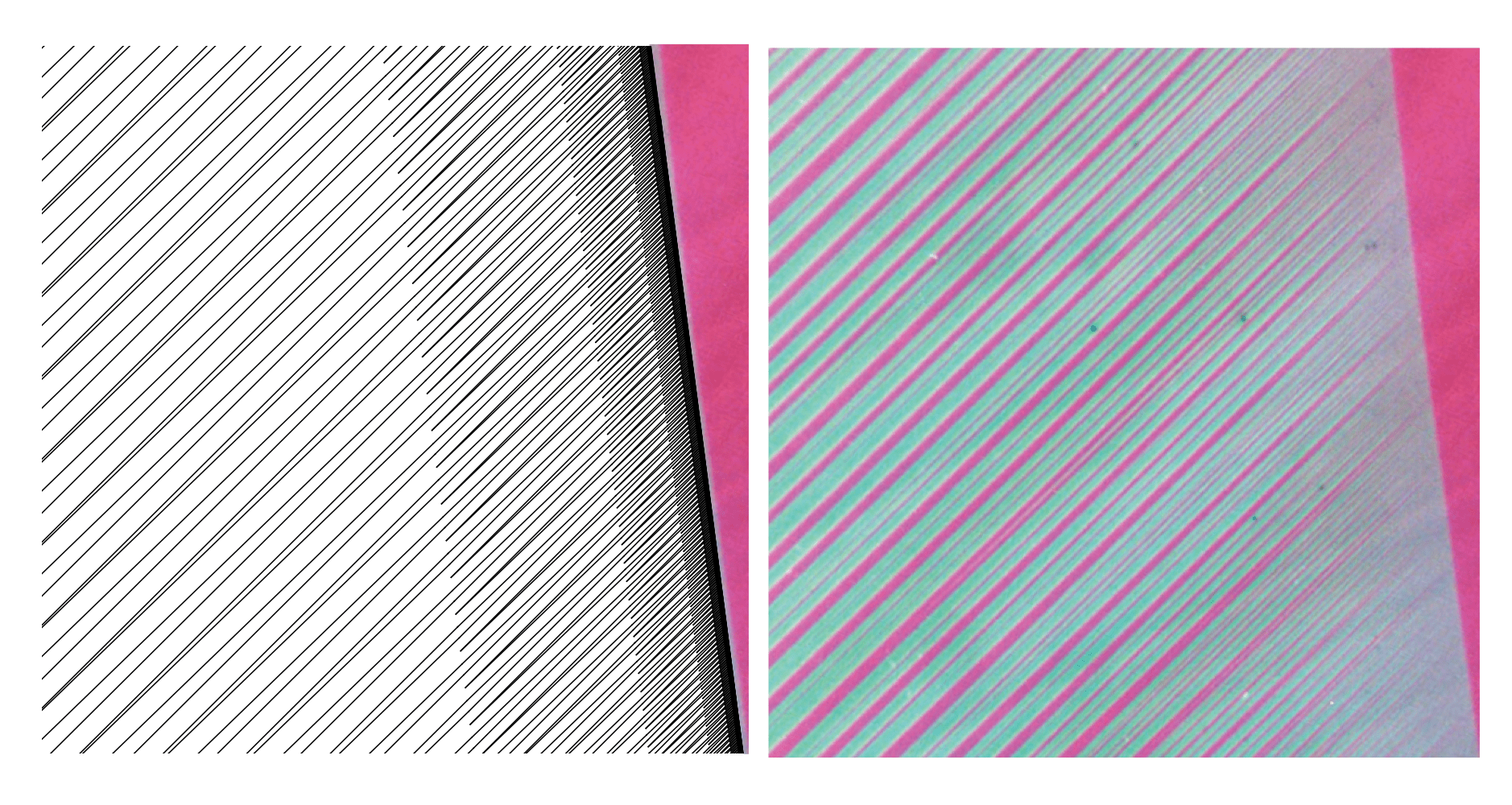
Characteristic microstructure exhibited by a shape memory alloy undergoing phase transformation (the experiment to the right is a CuAlNi sample courtesy of C. Chu). On cooling below a critical temperature, the martensite phase nucleates as fine-scale twins to accommodate that parent austenite phase at a habit plane. These twins often branch into finer and finer twins as they approach the interface. We developed a model to realistically capture the length scales and energy of this branching phenomenon. The left image is a simulation of the model consistent with the experimental parameters of the CuAlNi sample to the right.
-

Examples of nanotubes undergoing phase transformations through the propagation of kinematically compatible interfaces: helical interfaces (top) and horizontal interfaces (bottom). In both examples, the red and blue phases correspond to mirrored chirality. Thus, these interfaces are naturally interpreted as nanotube analogues of twinning — a feature common to bulk crystalline alloys.